Lagerbestand
Was ist Lagerbestand?
Beim Lagerbestand handelt es sich um die Gesamtheit aller vorhandenen Vorräte eines Unternehmens. Im Handel ist dies der Bestand an Waren, in Produktionsbetrieben der Vorrat an Roh-, Hilfs- und Betriebsstoffen, halbfertigen und fertigen Teilen sowie eventuell vorhandener Handelsware
Lagerbestand: Umfang & Ermittlung
Der Lagerbestand ist eine zentrale Komponente in Handels- und Produktionsunternehmen. Er versorgt Kunden oder die Fertigung stets mit den benötigten Rohstoffen, Waren oder Teilen und ist somit entscheidend für reibungslose Abläufe.
Erzeugnisse, die sich außerhalb der eigenen Räumlichkeiten befinden, können ebenfalls zum Bestand zählen, sofern der Gefahrenübergang noch nicht erfolgt ist. Dies ist insbesondere bei schwimmender, rollender und in Kommission gegebener Ware der Fall. Mengenmäßig wird der Lagerbestand durch Inventuren oder die fortlaufende Notierung aller Zu- und Abgänge ermittelt.
Die monetäre Bewertung kann nach verschiedenen Verfahren erfolgen. Häufig wird die Menge des vorhandenen Bestandes hierfür mit dem gleitenden Durchschnittswert der Ware multipliziert. Aus Sicht der Bilanz handelt es sich beim Lagerbestand um Vorratsvermögen bzw. Umlaufvermögen.
Der Lagerbestand (mengenmäßig) und der Lagerbestandswert bilden die Basis zur Berechnung wichtiger Lagerkennzahlen, auf die wir in diesem Ratgeber ebenfalls näher eingehen.
Was sind Mindestbestand, Meldebestand und Höchstbestand?
Zur Sicherstellung der optimalen Verfügbarkeit von Waren sind in der Lagerhaltung drei Parameter von wichtiger Bedeutung: der Mindestbestand, der Meldebestand und der Höchstbestand. Jeder dieser Werte muss sinnvoll berechnet werden, was anhand von Formeln erfolgen kann. Fehler bei der Festlegung können hingegen entweder zu einer Nichtverfügbarkeit von Waren oder zu einem Überbestand führen. Viele ERP-Systeme ermitteln die Wertigkeiten automatisch und regelmäßig anhand vorgegebener Rahmenbedingungen. Im Folgenden sehen wir uns die Definition genauer an.
Mindestbestand
Der Mindestbestand, welcher auch Sicherheitsbestand, Reservebestand oder eiserner Bestand genannt wird, hat die Aufgabe, unvorhergesehene Schwankungen der Bedarfe oder des Nachschubs auszugleichen. Auf diese Weise soll erreicht werden, den laufenden Betrieb aufrecht zu erhalten, auch wenn folgende Sachverhalte eintreten:
- Der Lieferant liefert nicht zum vorgesehenen Termin
- Die gelieferte Qualität entspricht nicht den Vorgaben
- Die Produktion stellt benötigte Erzeugnisse nicht termingerecht her
- Der Bedarf steigt ungewöhnlich stark an
- Es treten Fehlbestände auf
Die Wahl des richtigen Mindestbestandes richtet sich grundsätzlich nach der Wiederbeschaffungszeit (Bestellauslösung bis Wareneingang) und dem durchschnittlichen Tagesverbrauch, muss aber branchenspezifisch und aufgrund eigener Erfahrungen erfolgen. In der Praxis werden zur Orientierung folgende Formeln empfohlen:

Als generelle Formel für den Mindestbestand:

Beispiel: Du verbrauchst pro Tag 10 Stück einer Ware, die Wiederbeschaffungsdauer beträgt 5 Tage. Dein Mindestbestand sollte gemäß Formel 1/3 des Verbrauchs während der Wiederbeschaffungszeit betragen.
Mindestbestand= 50/3=16,66 Stück
Selbstverständlich können je nach Bedarf Parameter wie Lieferverzögerungen oder Mehrverbrauch in die Berechnung einbezogen werden.
Meldebestand
Wird der Meldebestand unterschritten, führt dies zur Auslösung einer Bestellung, weshalb hierbei auch vom sogenannten Bestellpunkt gesprochen wird. Er hat die Aufgabe, eine Bestellung von Waren rechtzeitig genug auszulösen, ohne dass der Mindestbestand angegriffen werden muss. Daraus folgt wiederum, dass die Parameter Mindest- und Meldebestand optimal aufeinander abgestimmt sein müssen. Wichtige Größen zur Berechnung sind auch hier die Verbrauchswerte und die Wiederbeschaffungsdauer. Die Formel stellt sich wie folgt dar:

Beispiel: Ein Handelsunternehmen verkauft pro Tag 3 Flaschen eines Rotweins. Die Wiederbeschaffungszeit beträgt 10 Tage, der Sicherheitsbestand liegt bei 25.
Meldebestand= 3 x 10+25=55 Flaschen Rotwein
Hieraus folgt: Sobald der Bestand 55 Flaschen unterschreitet, wird neue Ware nachbestellt. Im Optimalfall übernimmt dies ein ERP-System in Form eines Bestellvorschlags oder einer direkten Generierung einer Bestellung.
Höchstbestand
Der Höchstbestand, auch Maximalbestand genannt, hat in erster Linie die Aufgabe, unnötig hohe Vorräte zu verhindern. Die Begrenzung ist also einerseits im Hinblick auf die Kapitalbindung sinnvoll (insbesondere bei teuren Waren), andererseits aufgrund des zur Verfügung stehenden Lagervolumens gegebenenfalls zwingend notwendig (große, sperrige Teile). In die Berechnung des Maximalbestandes wird der Mindestbestand einbezogen. Die Formel lautet:
Höchstbestand=Mindestbestand+optimale Bestellmenge
Hieraus leitet sich ab, dass der Höchstbestand theoretisch anhand der kostenoptimalen Bestellmenge gewählt werden sollte. In der Praxis ist dies jedoch nicht immer möglich, da hierdurch eventuell eine zu hohe Kapitalbindung entsteht oder die Lagerkapazität überschritten wird. Eine automatisierte Berechnung des Höchstbestandes ist daher nicht immer zielführend. Legst du den Parameter jedoch manuell fest, musst du ihn laufend im Auge behalten und regelmäßig an die aktuellen Verbrauchswerte anpassen.
Wie kann der optimale Lagerbestand ermittelt werden?
Der optimale Lagerbestand muss oberstes Ziel der Disposition sein und verfolgt nachstehende Ziele:
- Reibungsloser Betriebsablauf
- Geringe Lagerkosten (Kapitalbindung)
- Kostenoptimale Beschaffung
Es stehen hierbei also mehrere Vorgaben zunächst in einem Konflikt zueinander, weshalb es gilt, den idealen Mittelweg zu finden. Zur Berechnung musst du zunächst die optimale Bestellmenge ermitteln. Eine rechnerische, relativ komplexe Lösung liefert hierfür die sogenannte Andlersche Formel:
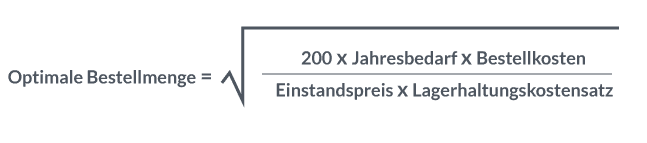
Beispiel: Der jährliche Bedarf eines Produkts liegt bei 50.000 Stück, die Bestellkosten liegen bei 20 Euro. Der Einkaufspreis pro Stück beträgt 5 Euro und der Lagerhaltungskostensatz 20 (%).
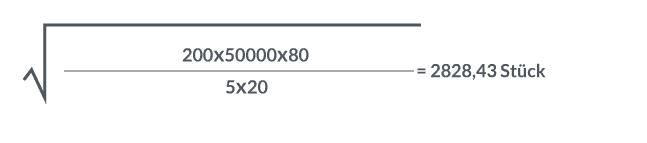
Die optimale Bestellmenge des Produkts liegt also bei rund 2828 Stück.
Jetzt kannst du den optimalen Lagerbestand anhand folgender Formel berechnen:
Optimaler Lagerbestand= Mindestbestand+optimale Bestellmenge
Beispiel: Gehen wir von einem Mindestbestand von 46 Stück und der oben ermittelten optimalen Bestellmenge von 2828 Stück aus, beträgt der optimale Bestand 2874 Stück (2828 + 46). Bei dieser Lagermenge sind sämtliche Kosten optimiert.
Lagerkennzahlen – Bedeutung und Anwendung in der Praxis
Im Lagerwesen existieren verschiedene Kennzahlen, mit denen du die Wirtschaftlichkeit, Versorgungssicherheit sowie Wichtigkeit von Artikeln im Bezug auf ihren Verbrauch oder ihre Kapitalbindung ermitteln kannst. Die wichtigsten Lagerkennziffern stellen wir dir im Folgenden vor.
Lagerumschlagshäufigkeit
Die Umschlagshäufigkeit gibt an, wie häufig sich ein Material im Lager verbraucht hat und durch Neueinlagerung wieder ersetzt wurde. Der Umschlag wird bezogen auf eine bestimmte Periode (meist 1 Jahr) berechnet. Es handelt sich hier also um eine Verdeutlichung der Beziehung von Verbrauch und Bestand. Eine Berechnung kann wert- oder mengenmäßig erfolgen. Die Formel stellt sich wie folgt dar:
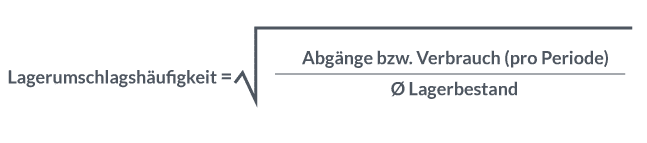
Beispiel: Von Artikel Nr. 4711 werden in einem Jahr 500 Stück aus dem Lager entnommen. Durchschnittlich waren 25 Stück auf Lager.
500/25=20
Ergebnis: Die Umschlagshäufigkeit beträgt 20. Das bedeutet: Der Artikel schlägt sich 20 Mal pro Jahr um.
Die Betrachtung der Umschlagshäufigkeit sollte nicht nur auf Artikelebene, sondern auch pro Materialgruppe und natürlich stets für das gesamte Lager erfolgen.
In der Praxis stellt sich nun die Frage, welche Lagerumschlagshäufigkeit als gut bezeichnet werden kann. Zwar wird in der Literatur häufig empfohlen, Artikel mit einer geringeren Umschlagshäufigkeit als 0,5 aus dem Bestand zu entfernen, als allgemeingültige Regel kann dies jedoch nicht gelten. Es könnte sich beispielsweise um ein schwer zu beschaffendes, wichtiges Ersatzteil handeln, welches trotz geringem Verbrauch unbedingt vorrätig sein muss.
Letztlich musst du die Umschlagshäufigkeit anhand nachstehender Empfehlungen individuell beurteilen und entsprechende Maßnahmen ableiten:
- Eine sehr niedrige Umschlagshäufigkeitbedeutet, dass die Lagerhaltung und somit die Kapitalbindung unnötig hoch und deshalb negativ zu bewerten ist. Senke bei betroffenen Artikeln den Bestand, verkürze die Lieferzeiten oder sorge für höhere Nachfrage bei den Kunden. Handelt es sich um Lagerhüter, versuche diese abzuverkaufen oder verschrotte sie notfalls, um die Mittelbindung zu entlasten.
- Eine hohe Umschlagshäufigkeitsagt aus, dass sich der Artikel jeweils nur kurz im Lager befindet. Grundsätzlich ist dies positiv, da hierdurch niedrige Lagerkosten erzielt werden. Ist die Umschlagshäufigkeit jedoch überdurchschnittlich hoch, deutet das auf zu geringe Bestände hin, die wiederum zu hohen Beschaffungskosten und ggf. zu Nichtverfügbarkeiten führen können. Ist dies der Fall, erhöhe die Bestände der betroffenen Teile moderat.
Praxistipp: Generiere über dein ERP-System regelmäßig (z. B. quartalsweise) Reports über dein gesamtes Sortiment, betrachte insbesondere die Ausreißer (extrem hohe und niedrige Umschlagshäufigkeit), und leite geeignete Maßnahmen ab.
Durchschnittliche Lagerdauer
Die durchschnittliche Lagerdauer liefert ein Bild über den aktuellen Stand und die Entwicklung der Kapitalbindung im Lager. Sie gibt Auskunft darüber, wie lange die Vorräte und damit das Kapital gebunden sind. Außerdem kann abgelesen werden, für wie viele Perioden der durchschnittliche Lagerbestand ausreicht, bis er theoretisch aufgebraucht ist. Die Formel lautet:

Beispiel: Ein Artikel aus deinem Sortiment ist durchschnittlich mit 20 Stück vorrätig, der Jahresverbrauch liegt bei 280 Stück.

Der Artikel befindet sich also im Durchschnitt etwa 26 Tage im Lager. Anders ausgedrückt: Der Vorrat reicht für 26 Tage aus.
Reduzierst du die Lagerdauer, hat dies eine Verbesserung deiner Wirtschaftlichkeit zur Folge, da gebundenes Kapital in liquide Mittel umgewandelt wird. Ist die Lagerdauer jedoch extrem niedrig, deutet dies auf zu geringe Bestände hin.
Lagerreichweite
Die Lagerreichweite wird in erster Linie dazu verwendet, um die interne Versorgungssicherheit innerhalb einer bestimmten Periode (Tag, Woche, Monat oder Jahr) zu beurteilen. Sie sagt aus, wie lange der Vorrat ausreicht, um den durchschnittlichen Verbrauch zu decken. Die Berechnung erfolgt mit dieser Formel:

Beispiel: Ein Artikel hat einen durchschnittlichen Lagerbestand von 100 Stück pro Tag. Täglich werden 20 Stück aus dem Lager entnommen.
100/20= 5 Tage
Ergebnis: Die Reichweite des Artikels beträgt 5 Tage. Erfolgt kein Nachschub, tritt danach ein Versorgungsengpass ein.
Sinkt die Lagerreichweite, so kann dies einen negativen Einfluss auf deine Produktion oder Lieferbereitschaft haben. Suche in diesem Fall nach möglichen Gründen, die beispielsweise in der Liefertreue des Lieferanten oder einer unzureichenden Disposition liegen können. Ist die Reichweite hingegen extrem hoch, deutet dies auf zu hohe Bestände hin. In diesen Fällen solltest du ebenfalls Gegenmaßnahmen einleiten.
Lagerbestände optimieren – allgemeine Tipps
Bereits in den vorangegangenen Kapiteln haben wir dir wertvolle Hinweise zur Optimierung deiner Bestände geliefert. In diesem Abschnitt erhältst du weitere allgemeine Tipps, die du in der Praxis anwenden kannst.
Die Ziele der Optimierung von Lagerbeständen sind:
- Senkung der Kapitalbindung
- Sicherstellung der Verfügbarkeit benötigter Materialien
- Kostenoptimale Beschaffung
Insgesamt sind zur Erreichung dieser Ziele mehrere Schritte notwendig. Folgende Maßnahmen eignen sich hierzu:
Handlungsbedarf identifizieren
Ermittle zunächst wichtige Lagerkennzahlen aus den vorangegangenen Kapiteln wie die Umschlagshäufigkeit, Lagerdauer und Reichweite. Betrachte sie zunächst in der Gesamtheit und dann auf Ebene von Materialgruppen oder Einzelteilen. Beantworte folgende Fragen:
- Wie haben sich die Kennzahlen im Zeitverlauf entwickelt?
- Wie sind die Kennzahlen im Vergleich zu branchenüblichen Vergleichsdaten zu beurteilen?
Stellst du negative Entwicklungen bzw. Abweichungen fest, muss ermittelt werden, wo der Handlungsbedarf konkret liegt.
ABC-Analyse durchführen
Bei der Betrachtung des Handlungsbedarfs solltest du dich auf wichtige Teile konzentrieren, um den Aufwand in Grenzen zu halten. Mithilfe einer ABC-Analyse kannst du die Teile identifizieren, welche mengen-, wert- oder verbrauchsmäßig am wichtigsten sind. Lege die Priorität zunächst auf die A- und B-Teile, betrachte erst danach die unwichtigeren C-Teile.
Lagerbestand verringern
Verringere den Lagerbestand bei Teilen mit niedrigen Verbräuchen oder hohem Bestandswert, indem du die Parameter Sicherheits- oder Höchstbestand korrigierst. Trenne dich außerdem regelmäßig und rechtzeitig von Lagerhütern. Du schaffst hierdurch Platz für dringender benötigte Materialien und verbesserst außerdem deine Liquidität.
Verfügbarkeit verbessern, Bestellkosten senken
Identifiziere deine Schnelldreher, also die Teile mit sehr hohen Verbräuchen. Weisen diese außerdem eine hohe Umschlagshäufigkeit auf, erhöhe gegebenenfalls den Höchstbestand. Hierbei erreichst du zum einen mehr Versorgungssicherheit und kannst auf der anderen Seite deine Bestellkosten reduzieren. Etliche Lieferanten bieten zudem Staffelpreise an, die erst ab einer gewissen Abnahmemenge zum Tragen kommen. Diese günstigeren Konditionen kannst du dann ebenfalls nutzen.
Disposition optimieren, Parameter richtig setzen
Optimiere insgesamt deine Disposition, indem du sie besser an die Verbrauchswerte der Vergangenheit oder die zukünftige Produktionsplanung anpasst. Verwende im besten Fall ein ERP-System, das eine (teil-)automatisierte Disposition ermöglicht, und automatisch Vorschläge für die optimalen Sicherheits-, Melde- und Höchstbestände liefert. Insbesondere bei einem breiten Sortiment ist dies fast unerlässlich.
Fazit: Enorme Optimierungen mit einfachen Mitteln möglich
In den meisten Handels- und Produktionsunternehmen stellen die Lagerbestände den größten Anteil des gebundenen Kapitals dar. Anhand weniger Kennzahlen kannst du objektiv beurteilen, ob eine Optimierung deiner Bestände erforderlich ist. Eine manuelle Vorgehensweise ist heutzutage dank moderner ERP-Systeme bzw. Warenwirtschaftssysteme glücklicherweise nicht mehr erforderlich. Bei großen Sortimenten sind das Bestandscontrolling und die optimale Disposition ohne IT-Unterstützung nicht mehr denkbar. Wenn du es dir zur Angewohnheit machst, deine Bestände regelmäßig anhand von Reports zu durchleuchten und daraus sinnvolle Optimierungsmaßnahmen abzuleiten, bist du in der Lage, trotz einer geringeren Kapitalbindung eine hohe Verfügbarkeit deiner Teile oder Waren sicherzustellen. Die Unternehmensleitung sollte hierbei stets einbezogen werden, damit die Lagerwirtschaft optimal in die Gesamtstrategie des Unternehmens eingebunden werden kann.
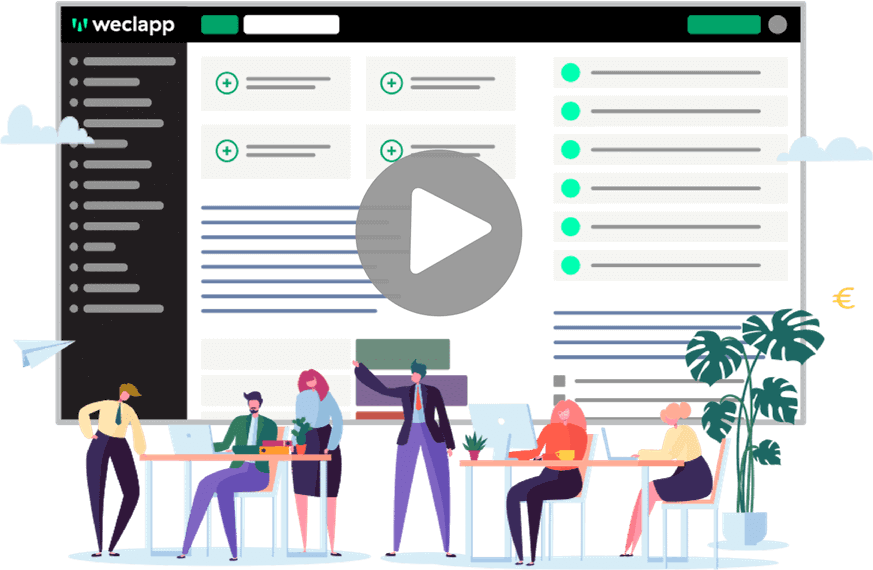
Spannende Beiträge rund um Unternehmertum, ERP, Buchhaltung, CRM und Software:
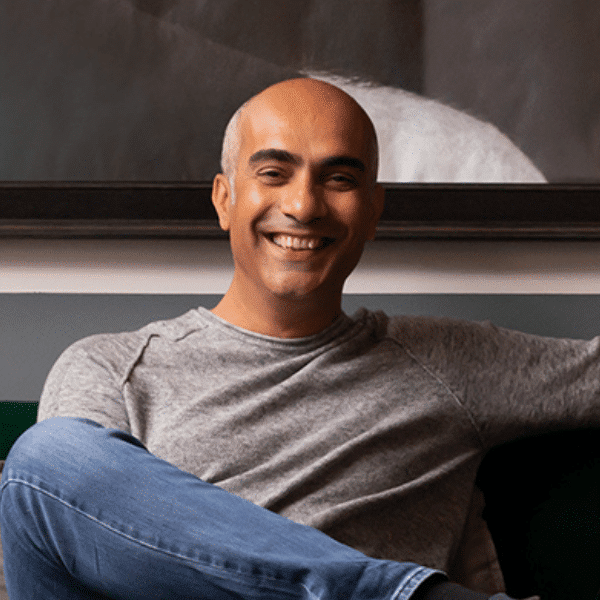
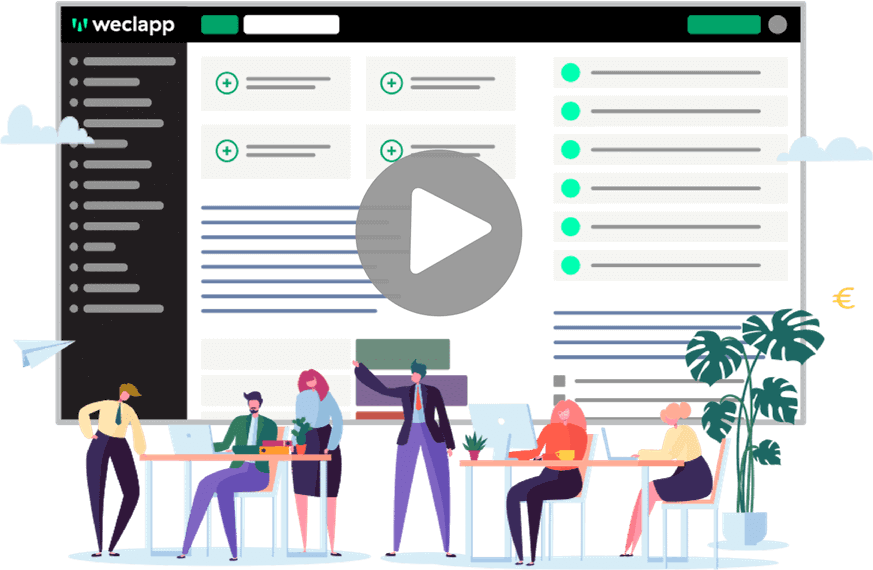
Spannende Beiträge rund um Unternehmertum, ERP, Buchhaltung, CRM und Software: